18 Van Buren St.
Low Income Modular Housing
RISD M.Arch Design
RISD M.Arch Design
Date: Autumn 2020
Location: Providence, RI.
Advised By: Johnathon Knowles, Brett Schneider.
Materials: Benson Wood prefab panels,
Vuscreen Livorno (outdoor fabric), Typ.
Location: Providence, RI.
Advised By: Johnathon Knowles, Brett Schneider.
Materials: Benson Wood prefab panels,
Vuscreen Livorno (outdoor fabric), Typ.

This project is in partnership with the City of Providence to create low cost modular homes for low-income families within Lower South Providence.
Neighbourhood
18 Van Buren Street is 1/30 plots of land currently owned by the City of Providence that can be gifted to local non-profits to make low-income housing. This particular plot of land is situated in Lower South Providence. This area is considered “the rough side of town”, with that being said, the area is starting to go through rejuvenation and gentrification. Many people have been moving to Providence in recent years from Boston due to increasing housing prices.
This area is populated by the traditional pre-1930s New England style triple-decker. A three-story all-wood home with a large balcony on the front of each building. The triple-decker usually lacks a front garden and often does not have a back garden either. Many triple-deckers have been renovated into multi-family homes.

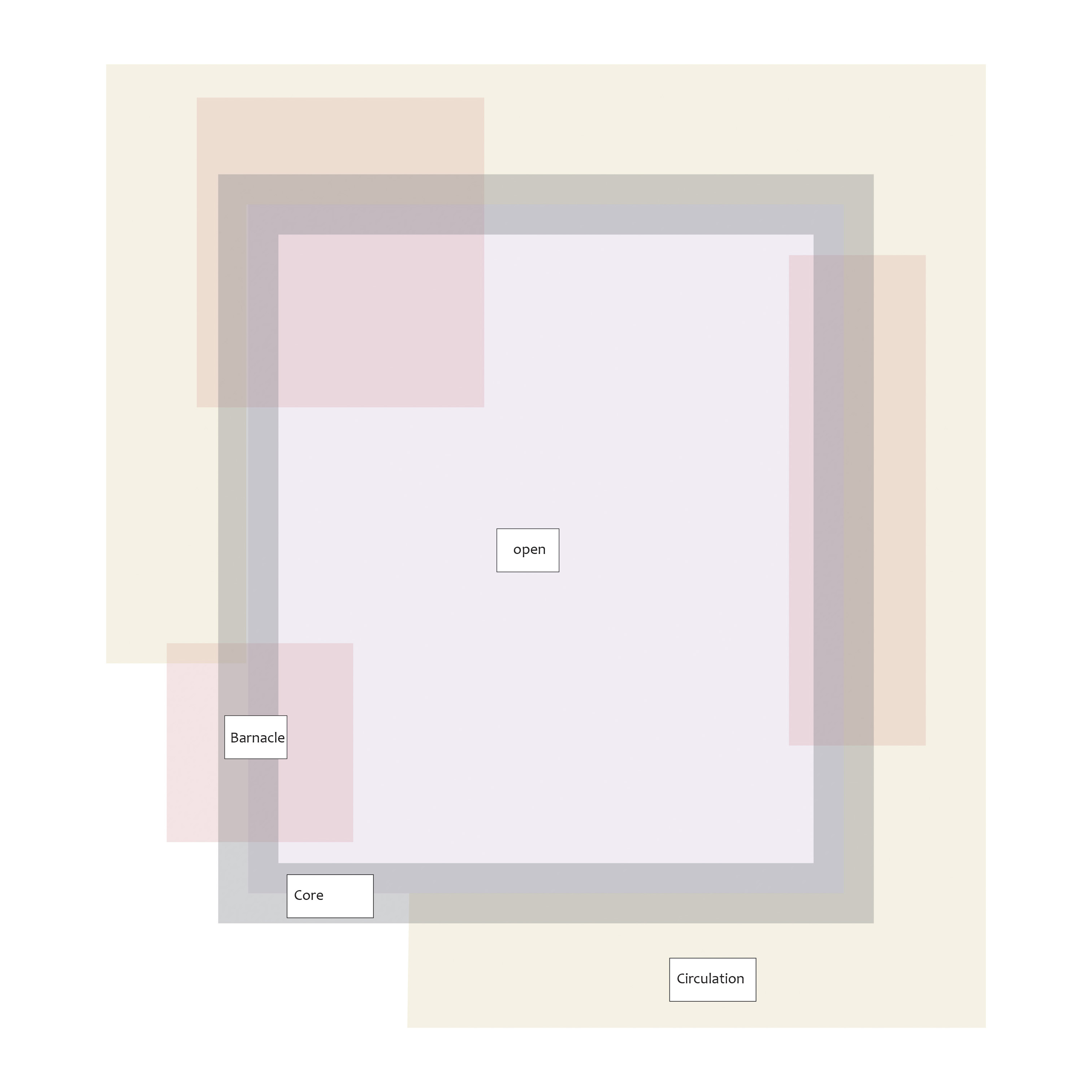
Concept
For this single-family home, there were several goals I wanted to achieve within the design. First, make sure that the house can be innovative but still fit in well with the neighbourhood. How do I create a triple-decker like house without wasting square footage? Secondly, how can I make this home easy to recreate and configure on various unique sites? Lastly, it’s impossible to reinvent the wheel, but can I do anything that might make the wheel cheaper to produce, more efficient, or reduce upkeep costs? I decided to use prefab wood to put the home together quickly, like a jigsaw, instead of typical 2x construction. Keeping the structure of the building within the prefab panels only made sense so I could then maximise the floor plan as much as possible. Then thinking about how I can cause “plug-in” type protrusions from the structural envelope for circulation and small jut-outs for built-ins, like the couch.
Interior Details
To maximise square footage while keeping the building compact, 18 Van Buren mimics the triple-deckers around it by maintaining a small footprint and using the square footage to contribute to the height rather than the width of the home. In addition, the staircase is expressed outside the building and cantilevered off from the structural Benson Wood prefab panels. This is to maximise useable floor space in the home.
To keep light within the home, aside from person-scale cosy windows in each “plug-in”, each floor has a light shelf to keep the entire area as naturally lit as possible as well as utilising a large skylight above. In addition, the fabric is stretched from the skylight above to each “mezzanine” single bedroom floor to create privacy and light diffusion.







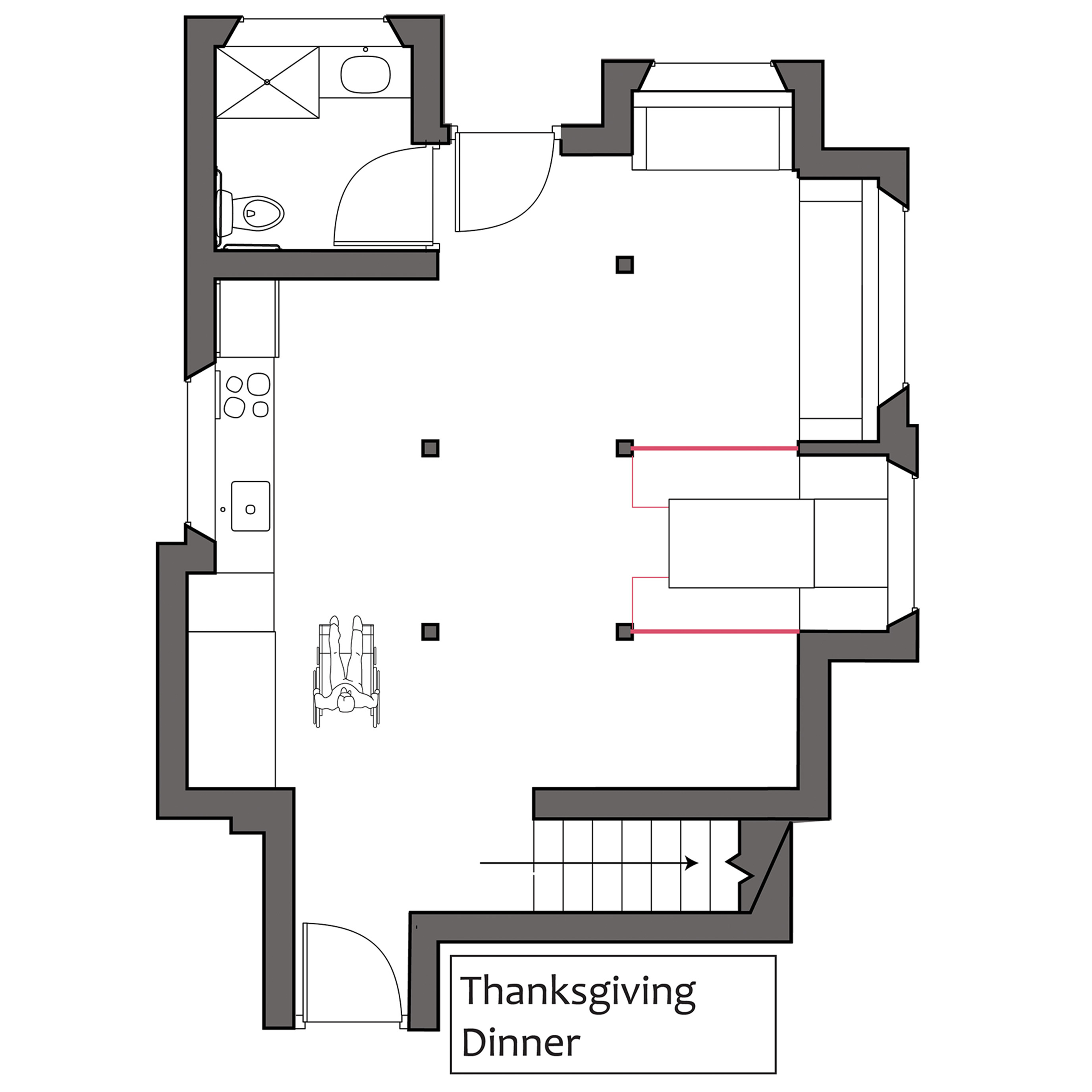

Construction Pt1.
While most of the structure for the building is located in the prefab walls, five columns exist within the living space. These columns serve two functions. The first is to provide additional support for the bedroom floors. The other is to provide places of connection for the ground floor “moveable walls”. The moveable walls are another instalment of the use of fabric within the home (whatever the family would like; they get to choose their wallpaper). The fabric spans from individual columns to create dividers in the open plan ground floor. This lets the ground floor become adaptable and can be used as an entirely wheelchair accessible apartment.
There are three steps in the imagined basic exterior construction of 18 Van Buren St. The first being assembling 16 prefab Benson Wood panels. The second step would be to add the “plugins”: the built-in living room, bedroom, and bathroom protrusions and staircase. The last step would be to cover the building with Swela’s Vuscreen Livorno fabric.


Construction Pt2.
Swela’s Vuscreen Livorno fabric is exciting. This fabric has two uses on the exterior of the home.
The upper of the fabric covers the area above the staircase to the roof. It is connected from the roof, pushed out by the light shelves and then connected to the top of the staircase. The idea is that there is no need for a gutter at the top of the home. Instead, the water flows down the fabric into a recessed channel hidden on the top of the staircase. This upper fabric is also another layer of light protection while diffusing light.
The lower fabric is clipped in and hangs from underneath the staircase. This clip-in system lets the fabric be readily removed whenever a storm is approaching, the owner wants to change/replace the fabric, or if the traditional wood siding of the home wants to be exposed.
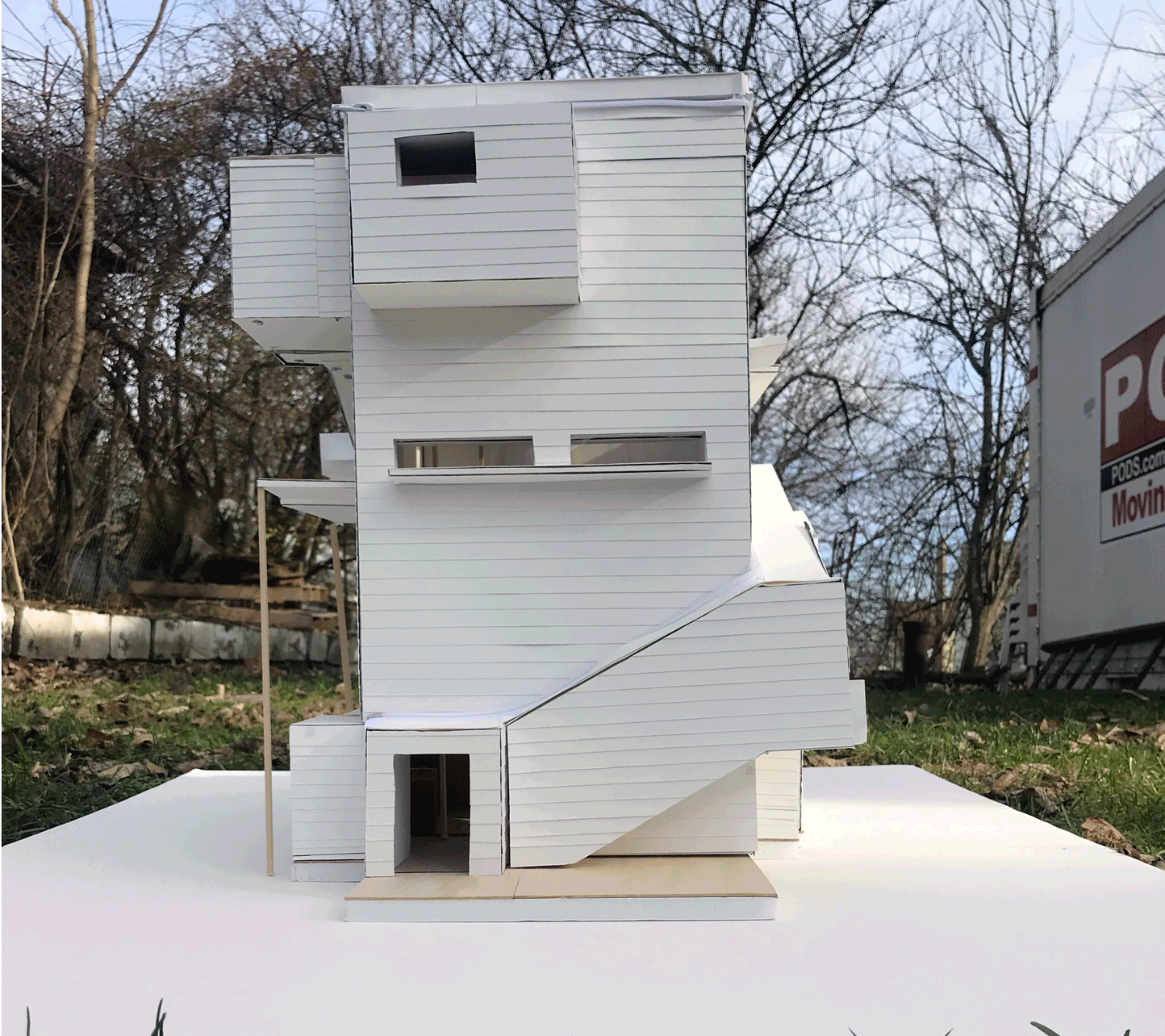
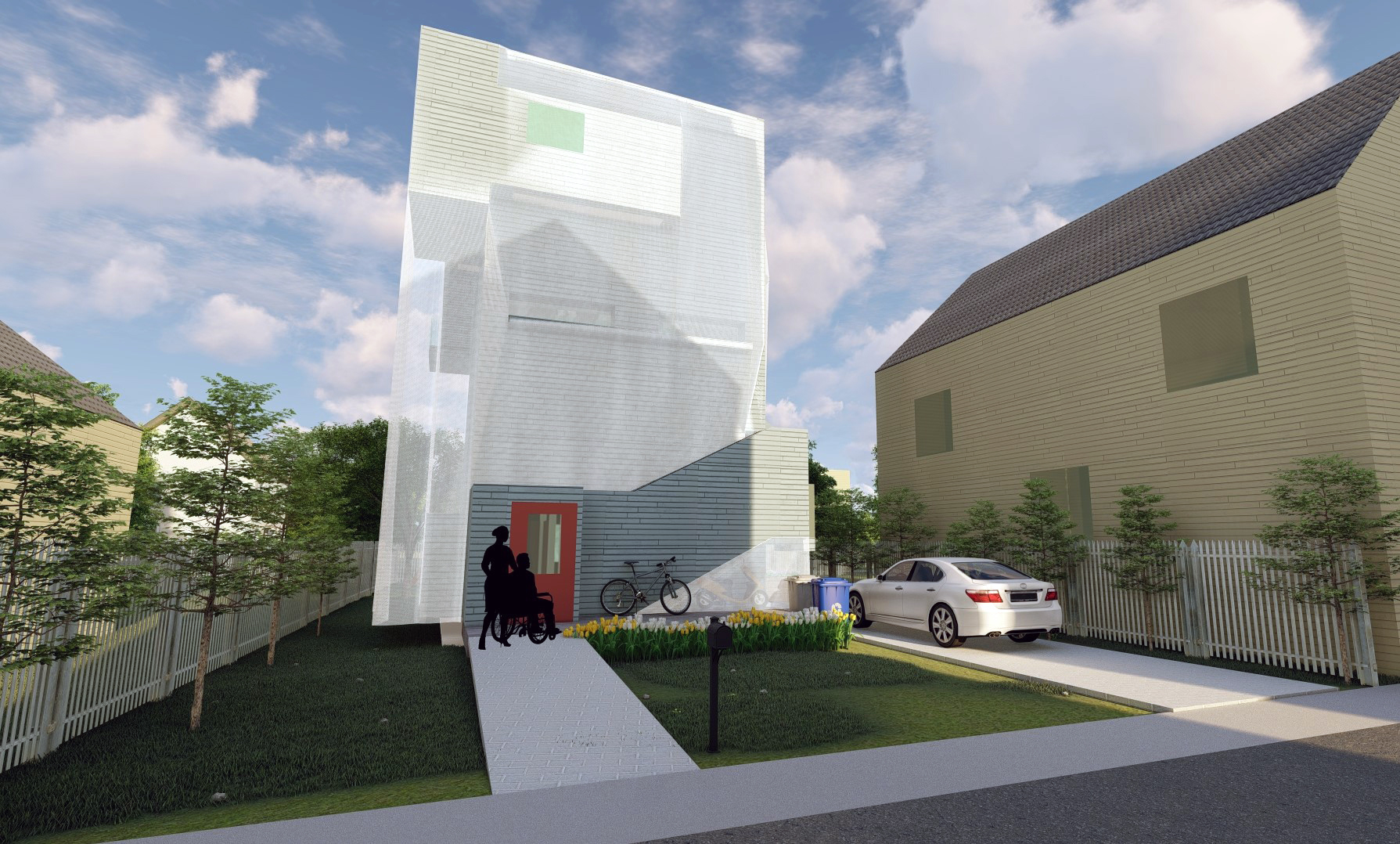


There is so much potential for discovery in new building material types.